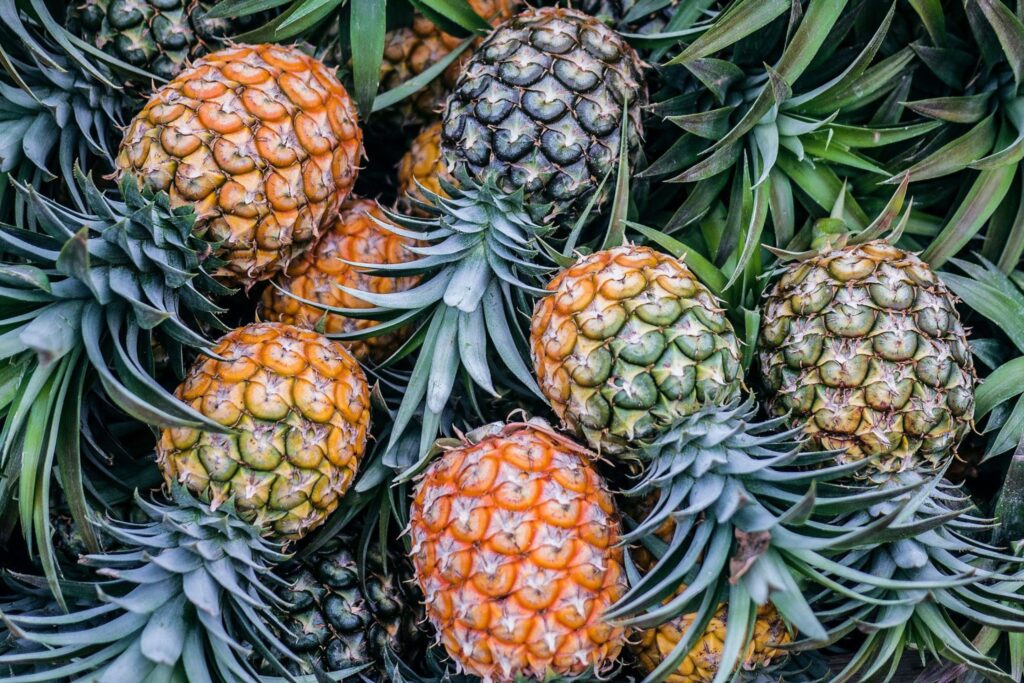
Case Study: Company Pineapple - Streamlining Inventory with Barcotech’s Hardware Devices
Published : 11/25/2024
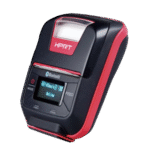
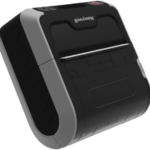
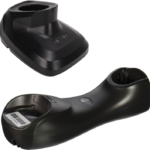
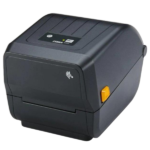
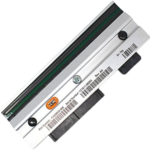
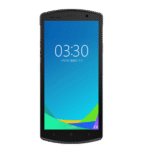
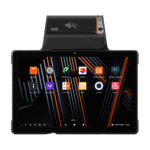
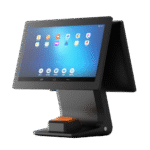
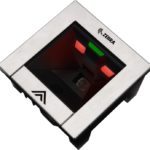
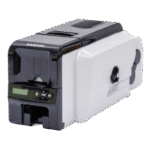
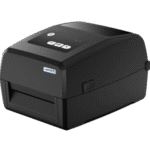
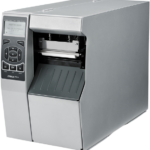
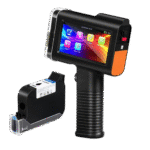
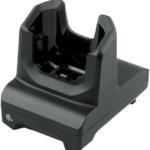
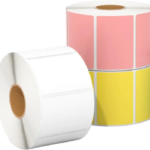
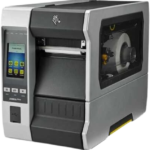
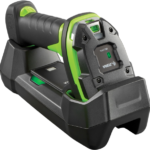
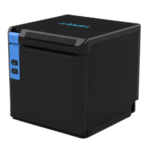
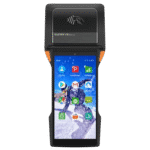
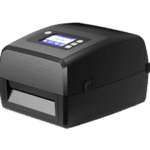
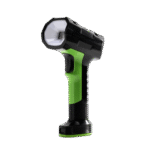
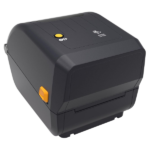
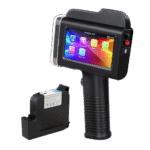
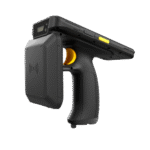
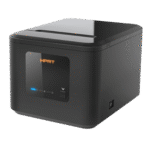
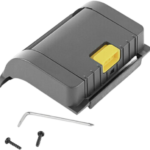
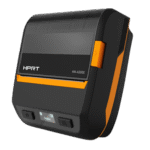
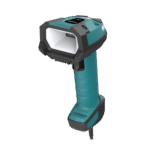
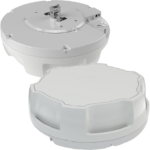
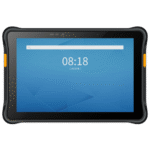
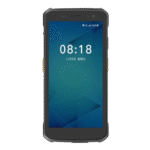
FAQ: How do I integrate my Barcode printer into my network?
Answer: All Barcode printers have the option to upgrade into Ethernet modules to connect to any network, Wireless, and LAN. However, the Industrial Printer normally comes with an Ethernet module included in the MLB
FAQ: How many meters of Ribbon can load in a Barcode Printer?
Answer: Options for label ribbon range from 75m to 450m
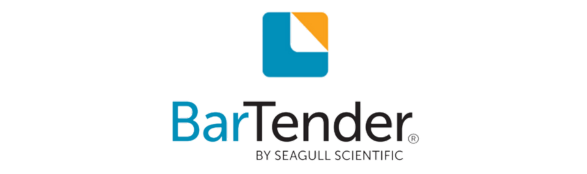
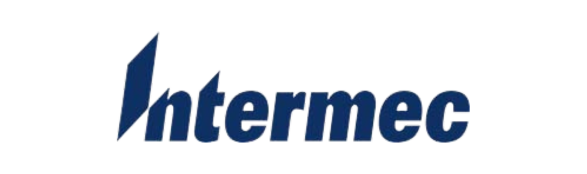
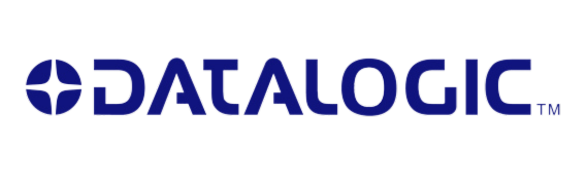
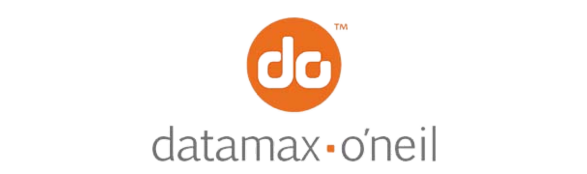
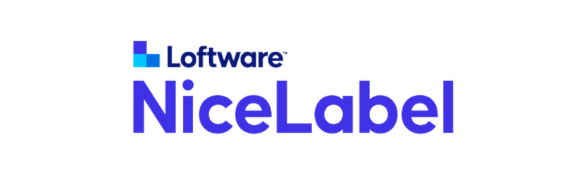
Company Background
Pineapple Company is a major producer and marketer of high-quality fresh fruit and vegetables, focusing on growing, processing, and exporting fresh and processed fruit products, especially pineapples and bananas. Based in the Philippines, Pineapple Company operates extensive pineapple plantations, particularly in the Mindanao region, and manages large-scale facilities for processing canned, juice, and dried fruit products.
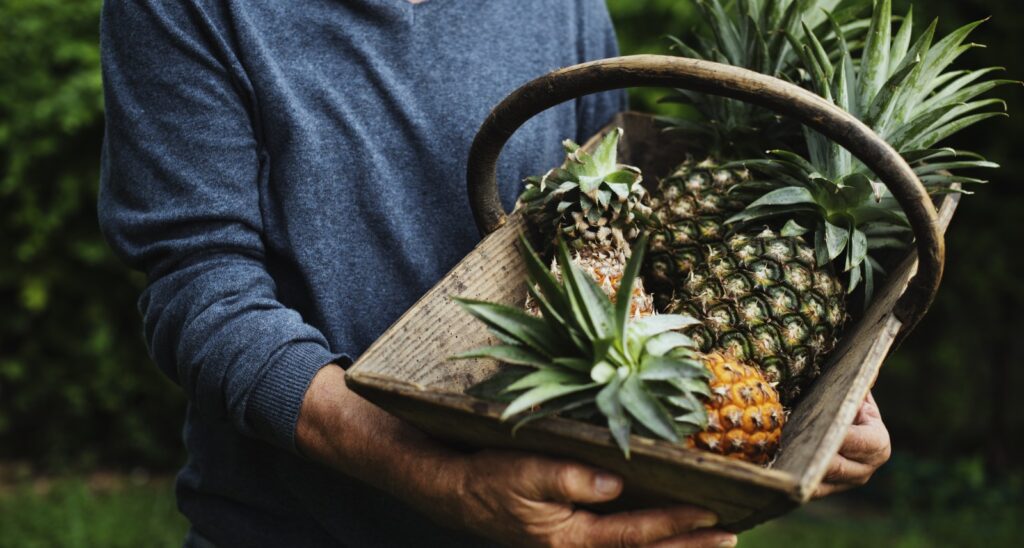
They are dedicated to the highest quality standards, providing people with nutritious, farm-fresh products that taste delicious and exceed expectations. Combining responsible farming practices, comprehensive programs for food safety pledged transparency, and state-of-the-art production, they give people the power to experience healthy living.
Problem Identification
The company faced challenges in optimizing its inventory processes to improve efficiency and reduce operational costs. Its reliance on commercial tablets and outdated scanners led to frequent delays, malfunctions, and costly replacements, as these devices were unsuited to the demands of an industrial setting.
By September 2023, Pineapple Company identified that the commercial devices’ lack of durability, limited read range, and incompatibility with cold storage environments were slowing inventory operations and increasing maintenance costs. These limitations highlighted the need for a more robust, reliable solution to streamline inventory management and support the company’s operational goals.
Solution Implementation
The implementation of the devices commenced in June 2024. The team worked closely with Zebra Technologies to ensure a smooth transition and proper training for employees. The rugged devices were seamlessly integrated into the existing warehouse management system, providing a more reliable and robust solution.
Device Selection
Pineapple Company decided to upgrade their devices by selecting two types of Zebra products: the Zebra MC9300 ultra-rugged mobile computer and the Zebra ET45 tablet, along with the Zebra Enterprise Browser for their system, to meet the demands of their industrial operations. These devices are renowned for their durability and are specifically engineered to perform reliably in harsh environments. Both units feature rugged construction that can withstand exposure to dust, moisture, and accidental drops, making them ideal for the heavy-duty conditions of manufacturing, warehousing, and logistics. The MC9300 is designed for barcode scanning and data capture in warehouse settings, while the ET45 tablet offers a versatile touchscreen interface, providing workers with real-time access to data, inventory management, and tracking on the go. Together, these devices not only enhance operational efficiency but also ensure continuous performance in the company’s demanding work environments.
Training and Implementation
Employees at the Pineapple Company underwent comprehensive training to ensure they could use the new devices effectively. Barcotech’s Technical Support team traveled to Davao to provide hands-on training to the staff on the proper operation of the Zebra MC9300 and Zebra ET45 devices. The training program lasted for two weeks, during which employees were introduced to the features of the devices, best practices for their use, and troubleshooting techniques. Following the in-person training, Barcotech continued to offer ongoing support through online. This online support allowed employees to reach out with any follow-up questions or clarifications they had about the devices, ensuring they had access to assistance whenever needed to maintain smooth operations.
Integration
By July 2024, the devices were seamlessly integrated into the company’s existing system, ensuring a smooth transition and minimal disruption to daily operations. As part of the integration process, the devices were aligned with the existing software infrastructure, enabling order processing, inventory tracking, and real-time data capture. This integration enhanced accuracy and efficiency by allowing employees to track shipments, update stock levels, and scan barcodes directly through the devices. As a result, Pineapple Company experienced improved workflow automation, faster processing times, and better visibility into inventory management, leading to an overall increase in operational efficiency.
Monitoring
To ensure the continued performance and effectiveness of the new devices deployed at Pineapple Company, Barcotech established a Davao Satellite office. This office not only allowed for closer monitoring of the devices’ functionality but also enabled Barcotech to better serve other clients located in the Mindanao region. In addition, with the assistance of our Technical Support team, Pineapple Company secured an extended warranty for their devices, providing added peace of mind and coverage. To further ensure smooth operations, a service unit was prepared and readily available to address any potential issues with the devices. This proactive approach allowed Barcotech to quickly resolve any problems, minimizing downtime and ensuring uninterrupted service for Pineapple Company.
End Results
As of September 2024, the Pineapple Company continues to benefit from the implementation of the Zebra devices. The company has seen an 80% improvement in inventory management efficiency, leading to significant cost savings and increased productivity. Upgrading to these advanced devices has been crucial in streamlining operations, reducing errors, and optimizing stock levels. Real-time data access and faster order processing have further enhanced overall performance. The Zebra MC9300 and ET45 devices have proven to be a durable and reliable investment, providing a strong foundation for the company’s ongoing operations and future growth